Contenido: Fundición a la arena, moldes, modelos, corazones y terminado. Procesos especiales de fundición. Procesos especiales de fundición. Bocas y canales de coladas. Fundido y vertido. Limpieza acabado y tratamiento térmico de piezas de fundición. Diseño de fundiciones.
Objetivo: Al finalizar la competencia describirá los fundamentos teóricos del proceso de fundición, sin error.
Fundición a la arena, moldes, modelos, corazones y terminado
El proceso para producir piezas u objetos útiles con metal fundido se le conoce como proceso de fundición. Este proceso se ha practicado desde el año 2000 AC. Consiste en vaciar metal fundido en un recipiente con la forma de la pieza u objeto que se desea fabricar y esperar a que se edurezca al enfriarse.
Para lograr la producción de una pieza fundida es necesario hacer las siguientes actividades:
- Diseño de los modelos de la pieza y sus partes internas
- Diseño del molde
- Preparación de los materiales para los modelos y los moldes
- Fabricación de los modelos y los moldes
- Colado de metal fundido
- Enfriamiento de los moldes
- Extracción de las piezas fundidas
- Limpieza de las piezas fundidas
- Terminado de las piezas fundidas
- Recuperación de los materiales de los moldes
Moldes temporales
Los recipientes con la forma deseada se conocen como moldes, éstos se fabrican de diferentes materiales como: arena, yeso, barro, metal, etc. Los moldes pueden servir una vez o varias. En el primer caso se les conoce como moldes temporales y los que se pueden utilizan varias veces, se les conoce como moldes permanentes.
Modelos desechables y removibles
Los moldes se fabrican por medio de modelos los que pueden ser de madera, plástico, cera, yeso, arena, poliuretano, metal, etc. Si los modelos se destruyen al elaborar la pieza, se dice que éstos son disponibles o desechables y si los modelos sirven para varias fundiciones se les llama removibles.
Fundición en moldes de arena
Uno de los materiales más utilizados para la fabricación de moldes temporales es la arena sílica o arena verde (por el color cuando está húmeda). El procedimiento consiste en el recubrimiento de un modelo con arena húmeda y dejar que seque hasta que adquiera dureza.
Fundición en moldes de capa seca
Es un procedimiento muy parecido al de los moldes de arena verde, con excepción de que alrededor del modelo (aproximadamente 10 mm) se coloca arena con un compuesto que al secar hace más dura a la arena, este compuesto puede ser almidón, linaza, agua de melaza, etc. El material que sirve para endurecer puede ser aplicado por medio de un rociador y posteriormente secado con una antorcha.
Fundición en moldes con arena seca
Estos moldes son hechos en su totalidad con arena verde común, pero se mezcla un aditivo como el que se utiliza en el moldeo anterior, el que endurece a la arena cuando se seca. Los moldes deben ser cocidos en un horno para eliminar toda la humedad y por lo regular se utilizan cajas de fundición, como las que se muestran más adelante. Estos moldes tienen mayor resistencia a los golpes y soportan bien las turbulencias del metal al colarse en el molde.
Fundición en moldes de arcilla
Los moldes de arcilla se construyen al nivel de piso con ladrillos o con materiales cerámicos, son utilizados para la fundición de piezas grandes y algunas veces son reforzados con cajas de hierro. Estos moldes requieren mucho tiempo para su fabricación y no son muy utilizados.
Fundición en moldes furánicos
Este proceso es bueno para la fabricación de moldes o corazones de arena. Están fabricados con arena seca de grano agudo mezclado con ácido fosfórico, el cual actúa como acelerador en el endurecimiento, al agregarse a la mezcla una resina llamada furánica. Con esta mezcla de ácido, arcilla y resina en dos horas el molde se endurece lo suficiente para recibir el metal fundido.
Fundición con moldes de CO2
En este tipo de moldes la arena verde se mezcla con silicato de sodio para posteriormente ser apisonada alrededor del modelo. Una vez armado el molde se inyecta bióxido de carbono a presión con lo que reacciona el silicato de sodio aumentando la dureza del molde. Con la dureza adecuada de la arena del molde se extrae el modelo, si este fuera removible, para posteriormente ser cerrado y utilizado.
También los procesos de moldeo pueden ser clasificados por el lugar en el que se fabrican.
1. Moldeo en banco. Este tipo de moldeo es para trabajos pequeños y se fabrican en un banco que se encuentre a la mano del trabajador.
2. Moldeo de piso. Para piezas grandes en las que su manejo es difícil y no pueden ser transportadas de un sitio a otro.
3. Moldeo en fosa. Cuando las piezas son extremadamente grandes y para su alimentación es necesario hacer una fosa bajo el nivel medio del piso.
Ventajas de los modelos desechables
1. Para la fabricación de moldes sin máquinas de moldeo se requiere menos tiempo.
2. No requieren de tolerancia especiales.
3. El acabado es uniforme y liso.
4. No requiere de piezas sueltas y complejas.
5. No requiere de corazones
6. El moldeo se simplifica notablemente.
Desventajas de los modelos desechables
1. El modelo es destruido en el proceso de fundición.
2. Los modelos son más delicados en su manejo.
3. No se puede utilizar equipo de moldeo mecánico.
4. No se puede revisar el acabado del molde.
Tolerancias en los modelos
En el diseño de los modelos que se utilizan para construir un molde es necesario tener en consideración varias tolerancias.
1. Tolerancia para la contracción. Se debe tener en consideración que un material al enfriarse se contrae dependiendo del tipo de metal que se esté utilizando, por lo que los modelos deberán ser más grandes que las medidas finales que se esperan obtener.
2. Tolerancia para la extracción. Cuando se tiene un modelo que se va a remover es necesario agrandar las superficies por las que se deslizará, al fabricar estas superficies se deben considerar en sus dimensiones la holgura por extracción.
3. Tolerancia por acabado. Cuando una pieza es fabricada en necesario realizar algún trabajo de acabado o terminado de las superficies generadas, esto se logra puliendo o quitando algún material de las piezas producidas por lo que se debe considerar en el modelo esta rebaja de material.
4. Tolerancia de distorsión. Cuando una pieza es de superficie irregular su enfriamiento también es irregular y por ello su contracción es irregular generando la distorsión de la pieza, estos efectos deberán ser tomados en consideración en el diseño de los modelos.
5. Golpeteo. En algunas ocasiones se golpean los modelos para ser extraídos de los moldes, acción que genera la modificación de las dimensiones finales de las piezas obtenidas, estas pequeñas modificaciones deben ser tomadas en consideración en la fabricación de los modelos.
Observe que cuando se utilizan modelos disponibles muchas de las tolerancias antes mencionadas no son aplicables.
Procesos especiales de fundición
Fundición en moldes metálicos

La fundición en moldes permanentes hechos de metal es utilizada para la producción masiva de piezas de pequeño o regular tamaño, de alta calidad y con metales de baja temperatura de fusión.
Sus ventajas son que tienen gran precisión y son muy económicos, cuando se producen grandes cantidades. Existen varios tipos de moldes metálicos utilizados para la fabricación de piezas por lo regular de metales no ferrosos, a continuación se mencionan algunos de las más utilizados.
1. Fundición en matrices
En este proceso el metal líquido se inyecta a presión en un molde metálico (matriz), la inyección se hace a una presión entre 10 y 14 Mpa, las piezas logradas con este procedimiento son de gran calidad en lo que se refiere a su terminado y a sus dimensiones. Este procedimiento es uno de los más utilizados para la producción de grandes cantidades de piezas fundidas. Se pueden utilizar dos tipos de sistema de inyección en la fundición en matrices.
· Cámara caliente
· Cámara fría
El procedimiento de fusión en cámara caliente se realiza cuando un cilindro es sumergido en el metal derretido y con un pistón se empuja el metal hacia una salida la que descarga a la matriz. Las aleaciones más utilizadas en este método son las de bajo punto de fusión como las de zinc, estaño y plomo. Las piezas que se producen son de 20 a 40 Kg. y se llegan a manejar presiones superiores a los 35 Mpa. Es un proceso rápido que se puede fácilmente mecanizar.
El proceso con cámara fría se lleva metal fundido por medio de un cucharón hasta un cilindro por el cual corre un pistón que empuja al metal a la matriz de fundición, las piezas obtenidas son de unos cuantos gramos a 10 Kg. y sólo es recomendable en trabajos de poca producción.
2. Fundición en cámara fría
Fundición con molde permanente por gravedad: Este tipo de fundición es utilizado para piezas en las que la calidad de terminado y dimensional no está sujeto a restricciones de calidad, debido a que la única fuente de energía que obliga al metal a llenar la cavidad del molde es la fuerza de la gravedad, un ejemplo de la utilización de este método el la fabricación de lingotes de metal.
La fusión de moldes de baja presión: Es un sistema de fusión que consiste en la colocación de un tallo sobre un crisol sellado, al inyectar presión al centro del crisol la única salida del metal fundido será el tallo por lo que se genera el flujo del metal por el tallo hasta que se llena la matriz y se forma la pieza.
Con este procedimiento se pueden fabricar piezas hasta de 30 Kg. y es rentable para grandes cantidades de piezas sin grandes requerimientos de calidad.
3. Fundición hueca
Es un sistema de producción de piezas metálicas huecas sin corazones fijos. Consiste en vaciar metal fundido en un molde que es volteado cuando se empieza a solidificar el metal. El metal que no se ha solidificado sale del molde para ser utilizado en otra pieza y el metal solidificado forma las paredes de la pieza. El resultado son paredes delgadas de metal.
4. Fundición prensada o de Corthias
Es un proceso para producir piezas huecas pero de mayor calidad que la fundición hueca.
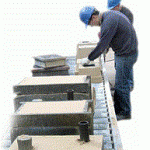
Se vacía una cantidad específica de metal fundido en el interior de un molde con un extremo abierto por el que se introduce un corazón que obliga al metal fundido a distribuirse uniformemente en todo el molde.
Una vez que empieza a solidificarse el metal del molde, se extrae el corazón, lo que origina una pieza de buena calidad.
Este sistema de fundición es considerado como artesanal y sólo es rentable cuando se van a fabricar pocas piezas.
Fundición centrífuga
La fundición centrífuga es un método en el que aprovecha la fuerza centrífuga que se puede en general al hacer girar el metal en tordo de un eje.
Existen tres tipos de fundición centrífuga:
I. Fundición centrífuga real
II. Fundición semicentrífuga
III. Centrifugado
Procesos especiales de fundición
Proceso de fundición a la cera perdida
Es un proceso muy antiguo para la fabricación de piezas artísticas. Consiste en la creación de un modelo en cera de la pieza que se requiere, este modelo debe tener exactamente las características deseadas en la pieza a fabricar.
El modelo de cera es cubierto con yeso o un material cerámico que soporte el metal fundido. Para que seque ese material cerámico se introduce a un horno, con ello el material cerámico se endurece y el modelo de cera se derrite.
En el molde fabricado se vacía el metal fundido y se obtiene la pieza deseada. Es un proceso que es utilizado para la fabricación de piezas ornamentales únicas o con muy pocas copias.
Proceso de cáscara cerámica
Es un proceso parecido al de la cera perdida, sólo que en este proceso el modelo de cera o un material de bajo punto de fusión se introduce varias veces en una lechada refractaria (yeso con polvo de mármol) la que cada vez que el modelo se introduce este se recubre de una capa de la mezcla, generando una cubierta en el modelo.
Posteriormente el modelo y su cáscara se meten en un horno con lo que el material refractario se endurecerá y el modelo se derrite. Así se tiene un molde listo para ser llenado con un metal y producir una fundición sólida o hueca.
Fundición en molde de yeso
Cuando se desea la fabricación de varios tipos de piezas de tamaño reducido y de baja calidad en su terminado superficial, se utiliza el proceso de fundición en molde de yeso. Este consiste en la incrustación de las piezas modelo que se desean fundir, en una caja llena con pasta de yeso, cuando se ha endurecido el yeso, se extraen las piezas que sirvieron de modelo y por gravedad se llenan las cavidades con metal fundido. El sistema anterior puede producir grandes cantidades de piezas fundidas con las formas deseadas.
Bocas y canales de coladas
Rebosaderos
Son orificios verticales que emergen a la superficie superior del molde, por los cuales asciende el metal fundido ; tienen el tamaño adecuado para que el metal contenido en ellos pueda permanecer fundido, hasta que haya solidificado y superado el periodo de máxima contracción el metal contenido en la fundición.
Se utilizan a menudo rebosaderos ciegos, que no se comunican con el exterior.
Aparte de los rebosaderos se pueden usar otros medios para realizar una solidificación adecuada aumentando el tamaño de ciertas secciones que de otra manera se enfriarían rápidamente. Otro método para acelerar el enfriamiento de secciones gruesas es el uso de coquillas metálicas, siendo de dos tipos externo o interno. Estas absorben rápidamente el calor.
Las internas están suspendidas por un alambre en la cavidad produciendo el enfriamiento pero luego quedan dentro de la fundición.
Canalización de la colada
Afecta directamente a la calidad de la fundición. Se usa mas de una boca conectándose estas con el bebedero por medio de canales pudiendo introducir el metal por varias a la vez, facilitando una solidificación direccional adecuada.
Fundido y vertido
Requisitos:
Temperatura adecuada
Economía
Prevención de contaminación
Mantenimiento de la temperatura
La mayoría de los metales se funden en un cubilote, horno de aire, eléctrico de arco, o de inducción.
Técnica de vertido

Para la transferencia del material del horno de fusión a los moldes se usan dispositivo vertedor o caldero. Teniéndose del tipo demango (manual) ,de caldera o tetera (mecánico), y el otro decaldero vierte directamente desde el fondo (para coladas grandes)
Vertido por presión: se fuerza el metal hacia arriba dentro del molde por medio de aire a presión.
Fusión y vertido en vacío: para obtener alta calidad las coladas son vertidas en una cámara de vacío. Otra variante usa un horno de arco que incluye un electrodo del mismo metal que se consume al fundir. Este método se utiliza para fabricar lingotes de titanio.
Fundición continua: es para producir un gran número de piezas con un solo molde.
Limpieza acabado y tratamiento térmico de piezas de fundición
La limpieza y el acabado de la pieza de fundición involucran todos o varios de estos procesos:
Quitar los núcleos
Eliminación de agujeros y alimentadores
Eliminar las escamas y rugosidades de la superficie
Limpiar la superficie
Reparar los defectos
En las fundiciones de no ferrosos y fundición de hierro, se sacan por medio de una piedra de abrasivos o por sierras de arco o continúas.
En piezas de acero, especialmente las grandes se eliminan los agujeros y rebosaderos por medio de una llama de oxiacetileno.
En la limpieza de la s piezas se usan cinceles neumáticos, amoladoras de mano o de pedestal. La limpieza superficial se logra por algún tipo de proceso de chorro con una sustancia abrasiva como la arena transportada con aire o con algún fluido.
Para corrección de pequeños defectos en las de acero se usa soldadura de arco.
Las piezas de fundición de acero se la someten casi siempre a un tratamiento de recocido.
Diseño de fundiciones
Deben evitarse interiores agudos ya que concentran tensiones.
Deben proveerse filetes generosos en todos los cambios de dirección y de sección, ya que estos reducen la concentración de esfuerzos y logran un enfriamiento y contracción uniformes.
Cambios bruscos de sección generan fallas durante el enfriamiento.
En la fundición en matriz es recomendable que la unión de estas sea en los bordes. Los espesores mínimos de sección de gran importancia en el diseño de cualquier tipo de fundición.
Fuentes: Apuntes de la materia de procesos de manufactura / unideg