Contenido: Proceso de reacción térmico. Proceso de reacción electrolítico. Proceso de reacción catalítico. Generalidades sobre el diseño de reactores. Clasificación de reactores químicos.
Objetivo: Al finalizar la competencia describirá los fundamentos teóricos de los procesos de reacción, sin error.
Proceso de reacción térmico
Los procesos de reacción térmicos desempeñan un papel de gran importancia, especialmente en química inorgánica y tienen lugar frecuentemente acoplados con reacciones de oxidación y reducción, Así sucede en la tostación, calcinación, caustificación, etc. En química orgánica se presentan en la preparación de combustibles gaseosos, en coquerías, en procesos de craquing, etc.
La gran cantidad de calor necesaria para su realización, se toma muchas veces de la reacción misma, pero también es frecuente suministrarlo desde el exterior con empleo de combustibles, sólidos, líquidos o gaseosos, de energía eléctrica y, algunos casos, utilizando directamente hornos de arco eléctrico.
En los numerosos procesos térmicos se desprende durante la reacción suficiente calor para que la reacción pueda tener lugar sin el suministro exterior de calor; muchas veces es incluso necesario eliminar parte del calor de reacción.
Este es el caso por ejemplo en la fabricación de cianamida de calcio a partir de carburo, en la producción de amoníaco sintético o de ácido sulfúrico de contacto, etc. Por lo contrario otras reacciones necesitan suministro de calor durante todo su transcurso, como en la calcinación de caliza, la producción de carburos, etc.
Los procesos de reacción que transcurren a alta temperatura se realizan en hornos, calentadores, reactores, etc. Las reacciones que desprenden calor se denominan procesos exotérmicos, y las que consumen calor endotérmicos.
Proceso de reacción electrolítico
La electrólisis es una reacción química provocada mediante corriente eléctrica continua. Los aparatos necesarios se denominan electrolizadores.
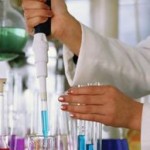
La transformación tiene lugar en los electrodos, de los que el dispositivo se llama ánodo y el negativo cátodo. Entre ellos debe de haber un electrolito para que tenga lugar conducción de corriente.
Si aquél es una disolución, el proceso se llama electrólisis en disolución y si es un fundido, electrólisis en fase fundida.
Las reacciones de electrólisis tienen aplicación en la descomposición de agua y sales, obtención de metales puros, tratamiento de superficies metálicas (cromado, etc.), procesos de oxidación y reducción, electrólisiscloro-álcali.
Realmente el electrolizador es una única célula de dimensiones relativamente pequeñas y que contiene todas las partes necesarias para una electrólisis: ánodo, cátodo y electrolito. 50 a 100 células se conectan para formar una serie, y una instalación electrolítica contiene varias series.
La construcción del electrolizador depende, en los detalles, de la reacción química a realizar, y así, por ejemplo, el material de los electrodos puede ser muy diferente.
En la purificación electrolítica de metales se utilizan cátodos de metal puro y se emplean como ánodos barras de metal impuro.
Es bastante común el empleo de electrodos de carbón (grafito), por ejemplo, en la producción de aluminio. En la electrólisis cloro-álcali se utilizan también cátodos de mercurio.
Si se requieren separar entre sí los productos de la electrólisis, es preciso subdividir la célula por medio de un tabique separador en un espacio catódico y otro anódico. Un tabique poroso de esta clase, solamente permeable para la corriente eléctrica, se denomina diafragma.
Tienen especial importancia en la electrólisis de disoluciones acuosas.
Proceso de reacción catalítico
Los métodos de procesos catalíticos de las clases más diferentes se han extendido paulatinamente por todas las zonas de la química técnica y constituyen hoy la base de las reacciones químicas más importantes y de mayor significación económica.
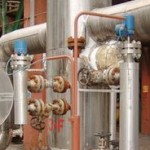
Se entiende por catalizadores, las sustancias que influencian la velocidad de una reacción química sin tomar parte estequiométrica en ella, pero en su acción es decisivo el contacto con los reactivos.
En la técnica, los catalizadores se utilizan para reacciones de síntesis y de degradación, para oxidaciones, hidrogenaciones, cloraciones, procesos con separación de agua, etc.
Como catalizadores se emplean ácidos, bases, metales, óxidos y sales metálicas, yodo, azufre, carbón, etc., en forma finamente dividida o depositada sobre pellets.
Algunos catalizadores tienen una zona de acción limitada y sólo puede emplearse en un limitado número de reacciones especiales; otros son de aplicación mucho más general.
En general, se espera de un catalizador: gran actividad, rendimiento constante, larga vida y fácil regeneración.
Algunos catalizadores orgánicos (biológicos) llamados enzimas o fermentos desempeñan un papel de gran importancia en los procesos vitales de organismo humanos, animales y de plantas.
Algunos de ellos, como la diastasa (de la cebada germinada) o los fermentos de la levadura tienen una gran importancia técnica en las industrias de fermentación.
Algunos de los procesos catalíticos tienen lugar a presión y se deben llevar en aparatos de presión denominados autoclaves.
Como todas los recipientes a presión, constan de materiales de alta calidad y de gran espesor de paredes. Se les reconoce las autoclaves exteriormente por las poderosas juntas y tuercas que unen la caldera y su tapa.
Generalidades sobre el diseño de reactores
La aplicación de fundamentos, teorías y datos de la física-química y de la catálisis al diseño de reactores químicos, constituye uno de los campos de mayor interés dentro de la ingeniería química. Indudablemente, uno de los puntos más importantes en la instalación de una nueva planta química, es el relativo al diseño del reactor a utilizar. Dicho diseño suele tratar de cubrir los puntos siguientes:
– Selección del mejor tipo de reactor o sistema de reacción para obtener una cantidad determinado del producto deseado.
– Determinación del tamaño óptimo del reactor o sistema de reacción.
– Establecimiento del mejor método de operación; es decir, fijar las variables de operación (presión, temperatura, composición de la alimentación, flujos, etc.) del reactor o sistema de reacción.
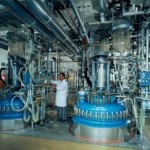
Estos tres aspectos, íntimamente relacionados entre sí, se refieren sólo a lo que se podría llamar diseño del proceso y no al diseño mecánico del equipo de reacción (tema que por supuesto, se aparta del objetivo de esta presentación).
Aunque el criterio más importante en la optimización del diseño de reactores es el económico, conviene, asimismo, tener en cuenta entre otros, los aspectos relativos a la disponibilidad de mano de obra y energía, a la seguridad laboral y a la protección del medio ambiente.
Los datos necesarios para diseñar un reactor son básicamente cuatro:
– Termodinámica de la reacción
– Cinética del proceso en las condiciones experimentales que puedan considerarse de interés
– Datos físico-químicos de las sustancias que intervienen en 1 sistema para el intervalo de condiciones en que se espere operar.
– Producción necesaria.
En ocasiones resulta, asimismo, necesario tener en cuenta la posible corrosión de los materiales de construcción, pues este hecho puede alterar las condiciones operacionales e incluso el diseño del propio reactor.
En general, los datos cinéticos que normalmente provienen de un estudio realizado a escala laboratorio (que indicará con bastante exactitud el efecto de las variables sobre la velocidad de reacción) no dan información sobre ciertos problemas para resolver a escala industrial (fenómenos de transferencia de materia, variación en la concentración de impurezas en el reciclado, distribución real de temperaturas dentro del reactor, etc.), por lo que, a veces, es necesario contar con la información suministrada por una planta piloto (que servirá asimismo, para comprobar la validez de la ecuación cinética desarrollada a escala laboratorio).
Clasificación de reactores químicos
La clasificación más elemental de los reactores es aquella que tiene en cuenta el posible intercambio de materia entre 1 sistema y el exterior. Se distinguen así tres tipos de reactores:
– Discontinuo (por lotes)
– Continuo
– Semicontinuo
Durante la operación del reactor discontinuo no existe intercambio de materia con el exterior. Se alimentan los reactantes de una vez, y cuando la reacción se ha efectuado se retira todo el contenido del reactor.
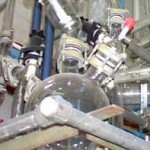
En este sistema la temperatura, presión y composición pueden variar a lo largo del tiempo de operación. En el reactor continuo la alimentación de los reactantes y la salida de los productos se hacen en forma ininterrumpida.
Las variables del sistema (cuando el reactor alcanza el estado estacionario) son independientes del tiempo. Si el reactor es de forma tubular, la variable independiente es la longitud del mismo a lo largo de la cual pueden existir variaciones de temperatura, presión y composición.
En el reactor semicontinuo, alguno de los reactantes o productos se alimenta o extrae continuamente mientras que el resto permanece en el reactor.
Así, por ejemplo, cuando la reacción entre dos líquidos entre dos líquidos es muy exotérmica, se prefiere cargar con uno de ellos el reactor y, enseguida, adicionar lentamente el segundo reactivo.
Esto ocurre en la reacción de amoniaco con formaldehído para producir hexametilentetramina, donde se añade lenta y continuamente hidróxido amónico al reactor cargado previamente con formaldehído.
En otro ejemplo, los reactantes están inicialmente en el reactor y uno de los productos se extrae continuamente, éste es el caso de las reacciones de esterificación, donde el agua o el éster se extrae por ebullición a medida que se va formando.
Otro caso de reactor semicontinuo se tiene en la cloracion de benceno líquido mediante cloro gaseoso para obtener monoclorobenceno, la corriente de cloro se adiciona continuamente al reactor cargado previamente con benceno, de manera que la concentración de dicho gas en el medio de reacción sea pequeña, con objeto de evitar la formación de productos policlorados. Estos reactores suelen operar en estado no estacionaria y w diseño ser relativamente complicado.
En general, los reactores discontinuos se utilizan en la producción de pequeñas cantidades donde presentan las ventajas de una gran flexibilidad de operación y un bajo costo de instalación.
Los reactores continuos, por su parte, se suelen emplear en producciones grandes, donde comparados con los reactores discontinuos, generalmente presentan las siguientes ventajas:
– Disminuyen los costos de operación al eliminar la carga y descarga de los reactores y facilitar el control automático.
– Mejoran el mantenimiento de la calidad del producto al ser las condiciones de operación más reproducibles.
La elección entre un reactor continuo y discontinuo estará, por tanto, íntimamente relacionada con la capacidad, los costos de instalación y los costos de operación (donde la mano de obra será muy importante).
La clasificación de reactores según su forma geométrica es también importante. Los reactores discontinuos o semicontinuos, por lo general se construyen en forma de tanques provistos de agitador. Las tres dimensiones del reactor suelen ser semejantes, con objeto de obtener un buen grado de mezcla y una distribución de temperatura uniforme y un menor consumo de materiales en su construcción.
Por su lado, los reactores continuos pueden tener la forma de tanque (similar al reactor discontinuo) o estar diseñados en forma tubular. En la figura 3.4 se han esquematizado los diversos tipos de reactores hasta ahora considerados.
Otra clasificación podría basarse en el método de operación de estos reactores con respecto a la temperatura:
– Isotermos
– Adiabáticos
– No isotermos
En los reactores isotermos se mantiene la temperatura durante la reacción, de manera que será necesario añadir o eliminar calor al reactor, según la reacción sea endotérmica o exotérmica, respectivamente. Este es el reactor más fácil de calcular, pero su utilización es limitada. La operación en condiciones adiabáticas supone un aislamiento total del reactor con el medio exterior.
Las variaciones de la temperatura, dentro del reactor, vienen determinadas por el calor de reacción.
En los reactores no isotermos, una cantidad de calor se añade o elimina del reactor, de manera que la temperatura no permanece constante durante el transcurso de la reacción. Este es el tipo de reactor más utilizado en aplicaciones industriales.
Fuente: Apuntes de la materia de procesos químicos / udideg